Joint venture partner for one Hybrid Industrial-waste Recycling Complex wanted
Joint venture partner for one Hybrid Industrial-waste Recycling Complex wanted
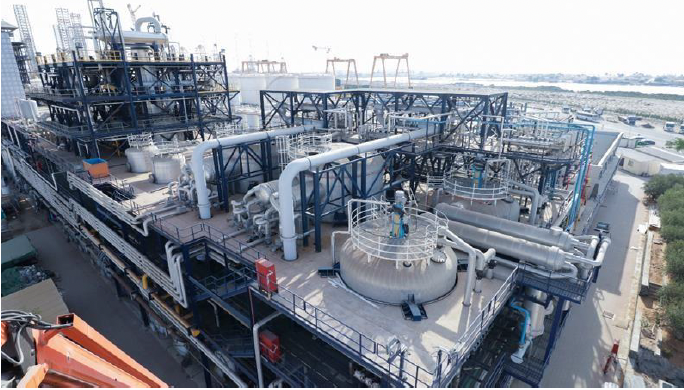
Processing capacity : 6,000m3/day Primary Feedstock : Heavy Aromatics, Naphtha, Solvent Naphtha, Condensate, ULO, HPO- Pyrolysis gasoline, opportunity / spot crude oil, Mixed Glycols, Full range Kerosene, White Spirit, Cutter Stock, PyGas, PFO.
Major Finished products : Gasoline Blend stocks, refined base oils, Gas-oils, BTX, Benzene, Toluene, Xylene (mixed), Aromatic Solvents, EB (Ethyl Benzene), MEG, DEG, TEG, mixed glycols and Cutter-stock
HIRC Open Art premise:
Functional objective of HIRC –Hybrid Industrial Recycling Complex is to handle
hydrocarbon and Power/Auto industry waste streams of the whole ME region.
However heavy crudes like Darr, Nile, & Chad crudes from North Africa, Escalante
Crude from Argentina also could also fill the feed gap. The complex is installed with a
versatile treatment cum distillation plant unit through a unique hardware
configuration. All the process units are purpose built with Open Art engineering and
techniques to handle different feed stocks of varying qualities. No Licensed
processes, or process technologies have been employed so far. No catalyst systems
are currently installed. Also there are no licenced or non-licensed processes in the
complex that fall under IP regime. The complex has been built for a very wide
varieties of feeds from glycols, UEO, Py-Oils, Hy Crudes. Situated inside Hamriya Free
Zone, the facility is named as HIRC –Hybrid Industrial Waste Recycle Complex,
Sharjah UAE. The in-house project team has erected the plant in different stages, first
being Tank farm, then Module-1, and Module-2. MODULE 1 portion of the complex,
complete in all respects as fully open art engineered. All units in Module 1 are with 4
batch process kettles, of which the distillation section has been purpose built with
two types of hardware, like 2 for mild vacuum and 2 for high vacuum operations.
The Module 2 portions are built for distillation and extraction operations of heavy
feeds, and glycols & BTX separations. Though they are still pending for mechanical
completion the design is open art engineering jobs.
A hydrotreating process would be the first of a technological component if brought
to site in future. Based on the current fuel market specs, this Sulphur removal, and
polishing would become a necessity.
Hardware description:
A feed and product tank farm with total storage capacity of 56,000M3 with 18 feed
and products storage tanks and 13 nos of intermediate day tanks at present. Tank
farm sections were erected in stages as early since 2008 period. Tanks are dome roof
type and internal floating type for products storage. An additional leased storage
tank of 100K M3 capacity is available for company use at 4 km away from HIRC site.
This additional facility is connected to seaport with draft 14+ m to handle vessels
above 65KT.
The site storage facility is connected to Port inner berth through
4(four) nos of 8’’ import/export pipelines with pigging capability. This was
operational since Y2008.
The utility and auxiliary systems for the process plant are also erected, such as CNG
Captive power plant of 12MW, 16 nos of package type Thermic boilers, 2 nos Steam
boilers, a Nitrogen plant, circulating fresh water cooling water tower train with
maximum flow of 4300M3/h, Chiller facility good enough to handle all products
without fugitive emissions, and 6 nos of Truck weighing gantry with dispensing
systems, all fitted with Mass flow meters. Fire & Safety full ring covering the entire
area were also erected and tank farm portion commissioned. Emergency diesel
pumps are also connected with fire water ring.
Process plant additions to functional tank farm were erected in two modular form,
Module 1 &2 before 2019. The Module-1 facility was entering commissioning stage
pending to completion of I&C jobs initiated in June 2019. Activity was stalled during
covid period, remains so until now. As mentioned earlier, Module-1 is designed to be
handling batch processing of broadly three to four types of feeds with significant
quality and quantity variations.
Operability description:
The whole plant configuration is custom designed for processing such semi-finished,
difficult to treat type industrial liquid waste streams and heavy crudes to near
purification or saleable quality products. Owing to quantity and quality variations of
the feeds batch processing has been generally adopted. However there exists
flexibility to convert batch distillation units to continuous processing mode. The
sources would also vary a lot but principally they are sourced through local UAE
channels as well as from KSA. However in future, a wider list of such hydrocarbon
waste streams and hy crudes such as Dar/Nile, Used cooking oils, Tyre pyrolysis oil
etc would also add to existing feed basket. All such feeds are proposed to be through
contracted importation to the plant site. Being open art engineered, the plant could
handle a wide variety of feed streams except that of high RVP feed stocks. Among
possible feed stocks low RVP crudes comes Dar, Nile blend to mention two for
processing. This document highlights processing scenarios for below waste streams
through Module-1. A process modelling outcome is also presented.
Petrochemical by-product Hy- Pygas- wide ranges, & Tyre Pyrolysis oils
BTX streams and Hy Reformates
Used Engine Oils and all Spent lubricant oils
Spent and contaminated Glycols (MEG/DEG/TEG).
Once operational, the front-end throughput of Module 1 is supposed to handle
maximum of 2500M3/D of different feeds on turn basis.
As of the current status the plant configuration can be made operational with the
above feeds without any major modifications or additions
Review of Circular Processing Merits and Effectiveness of operation.
The process complex is projected to improve the region’s circular uses, while making
a partial switch from fuels to chemicals for the region and export needs. Glycols and
BTX stream processing is feasible and they are complementing to circular uses
Being industrial waste streams, none of the methods, nor the processes are licensed,
technology bound. Coming to fuel regime, IMO 2020 calls for low sulphur fuels and
hence UEO/Py-Oils and Hy High TAN crudes as mentioned above would make good
synergies to meet low sulfur fuel product regime. All the products are a mix of fuels
but chemicals make the margins high.
The process methods as designed as open art engineered, are below units
1. De-Metalation K1101/2/3/4: Heating UEO mixed with a suitable coagulant in
batch wise kettles to precipitate down all the inorganic as well as organic
metals and Settling in Silo Tanks. Residue ash value correction and organic
metal removal from UEO are the targets.
Process is customary, and does not require any license or catalyst technology.
2. Dehydration K1201/2/3/4: This is typical distillation process in four batch
wise kettles where in feed is heated to dehydration temperature around 120-
deg C and flashed under mild vacuum. Water is separated at overheads.
Dehydrated Oil is stored in insulated tanks or directly vacuum distilled.
Process is open-art and does not require any license, technology special
machinery.
3. Vacuum distillation K1301/2: The dehydrated, UEO is distilled in two batch
kettles to physical Vacuum separation of Base Oil fractions as LV and HV base
oil range cuts. Vacuum distillation Process also removes light fractions in top
and hy fractions at bottom. Vacuum is generated by three stage steam
ejectors with inter and after condensers. Base oil fractions are further
purified in Extraction Units to specifications by removing Aromatics by
Solvent extraction later.
Process is typical batch distillation, open-art & does not require any license or
technology.
4. Aromatic Extraction Unit K1601,2,3/4,5,6/7,8,9: The LV(Light Vacuum oil)
and HV(Heavy Vacuum oil) oils obtained from Vacuum distillation Unit are
separately transferred to silo tanks and from there fed to Aromatics
Extraction Kettles in any of the three group of extraction kettles for solvent
extraction of Aromatics from LV and HV oils. Aromatics extraction is carried
out by a Solvent called NMP (N-Methyl-2 Pyrrolidon) at a suitable solvent
feed ratio. The process is performed in batch kettles of 3 each working in
tandem, supported by right solvent to feed ratio, agitation, optimum
temperature and 2-4 hours of extraction time. The mixture is then decanted
to settling tanks, where Raffinate(Base Oil) portion would float as distinct
clear top layer and dark bottoms layer as Extract(Solvent, and Aromatics
mixture)
Process is open-art engineered extraction process as practised by numerous
base oil recycling plants globally. This too does not require any license,
technology or special machinery. However the solvent NMP is universally
accepted and used for extraction process here is skill based.
5. Cracker Unit K1501/2/3/4 or High temperature distillation unit
From the decantation tanks the extract residue bottoms, known as extract
will be taken to Cracker Unit batch kettles of 4 nos. In cracker kettles
operated at top temperature of 195-220 degC, the solvent removal from the
extract would be complete with same purity as feed. The pure solvent is
separated as top product and is then recovered and sent to solvent tank for
reuse. The expected Solvent losses from the process is below 0.02% max.
The bottoms product is mostly heavy aromatics that finds value in fuel or as
solvent uses.
Process is typical of a Solvent Recovery unit in batch distillation, post
aromatics extraction. Process is open-art & does not require any license or
technology.
6. Solvent stripping Unit k1601/2/3/4:(Base Oil purification)
The non-aromatics component decanted from Extraction Unit and stored in
separate tank is taken to Stripping Unit to strip out the traces of Solvent by a
suitable stripping medium such as steam or (Nitrogen) in the batch stripping
kettles. Initially the traces of solvent and water will be condensed and
followed by clear, aromatics free, color free, solvent free, pure base oil would
be the premium product.
Here too, Process is typical of a Solvent stripping unit as in batch distillation,
open-art & does not require any license or technology.
7. Refluxed batch distillation Unit:(Hy Crudes distillation & Glycols
purification)
This unit has two SS kettles and on top of each, there is packed column of 12
m extra height. This column could make batch operation for spent glycol
dehydration as well as Heavy Crude distillation. The typical feeds are used,
degraded glycols with water contamination, Hy Crudes like DAR Crude (HAC)
etc.
This Process is also typical of a distillation for minimal overheads removal for
flash point & RVP correction as well as water removal. The unit is suitable for
heavy crude or contaminated glycol processing in batch distillation. Open-art
engineering & does not require any license or technology.
Vetting guidelines
All the units are straightforward physical processes and can be operated by
experienced refinery operations team. There is a question regarding assurances or
guarantee of process efficiency and capacity. The answer is Vetting job. Here vetting
by an either global engineering company or a designing company specialized and
experienced with similar plant designs, EPC and commissioning would be desirable.
Latter option would be the best to clear ambiguities around.
Towards this has recently completed the Feed Assays prior to an engineering
revalidation. An experienced engineering company shall be assigned to completing
residual engineering, data generation and drawings of the Module 2. This exercise is
in the interest of potential future partners/owner.
The Joint Venture Partner of this Hybrid Industrial-waste Recycling Complex have to invest at least 80 million USD. Please contact us for further questions
TCME Investments & corporate financing team.
——-
We help and work with several governments around the world to make such private partnership projects possible or even search for big Projects, the right Joint Venture Partner. If you as an investor have any further questions about this project, please contact us.
TCME – Group worldwide is a leading professional International Business Investment and Advisory Firm for Foreign Economic Relations, with 17th. departments in different Countries around the world and the Headquarter in Malaysia.
GCI UNIT Worldwide, designs and implements customized, holistic strategies for successful investors and entrepreneurs to legally reduce their tax bills, diversify and protect their wealth, invest abroad, gain a second citizenship and live a freer life worldwide to lead.
YOUR CHANCE FOR A BETTER LIVE
GCI Unit Worldwide firm is a professional International Business Investment and Advisory Firm for Foreign Economic Relations. Our range of services includes:
• Offshore and Onshore Company Formation,
• executive Search,
• IT & Cyber Security Protection
• African Gold & Diamonds
• international Business & Management
• Citizenship & Residency
• Investments & Corporate Financing
• Mining and Trading
• Advisory for Foreign Economic Relationship
• Diplomatic Consultancy & Public Affairs
If you would like to discuss your internationalization and diversification plans, book a consulting session* or email us under: [email protected]
*A counseling session is a conversation about your portfolio and goals. It does not constitute legal, financial, tax or investment advice.
Department GCI – Unit Global Citizenship Investment (GCI Unit worldwide)
by TCME Worldwide Group – Global Investments –
Level 33, Ilham Tower, 8 Jalan Binjai,
Kuala Lumpur 50450, Malaysia
www.tcme.company
www.citizenship-news.com
Phone: +66 99091 8357 also for WhatsApp